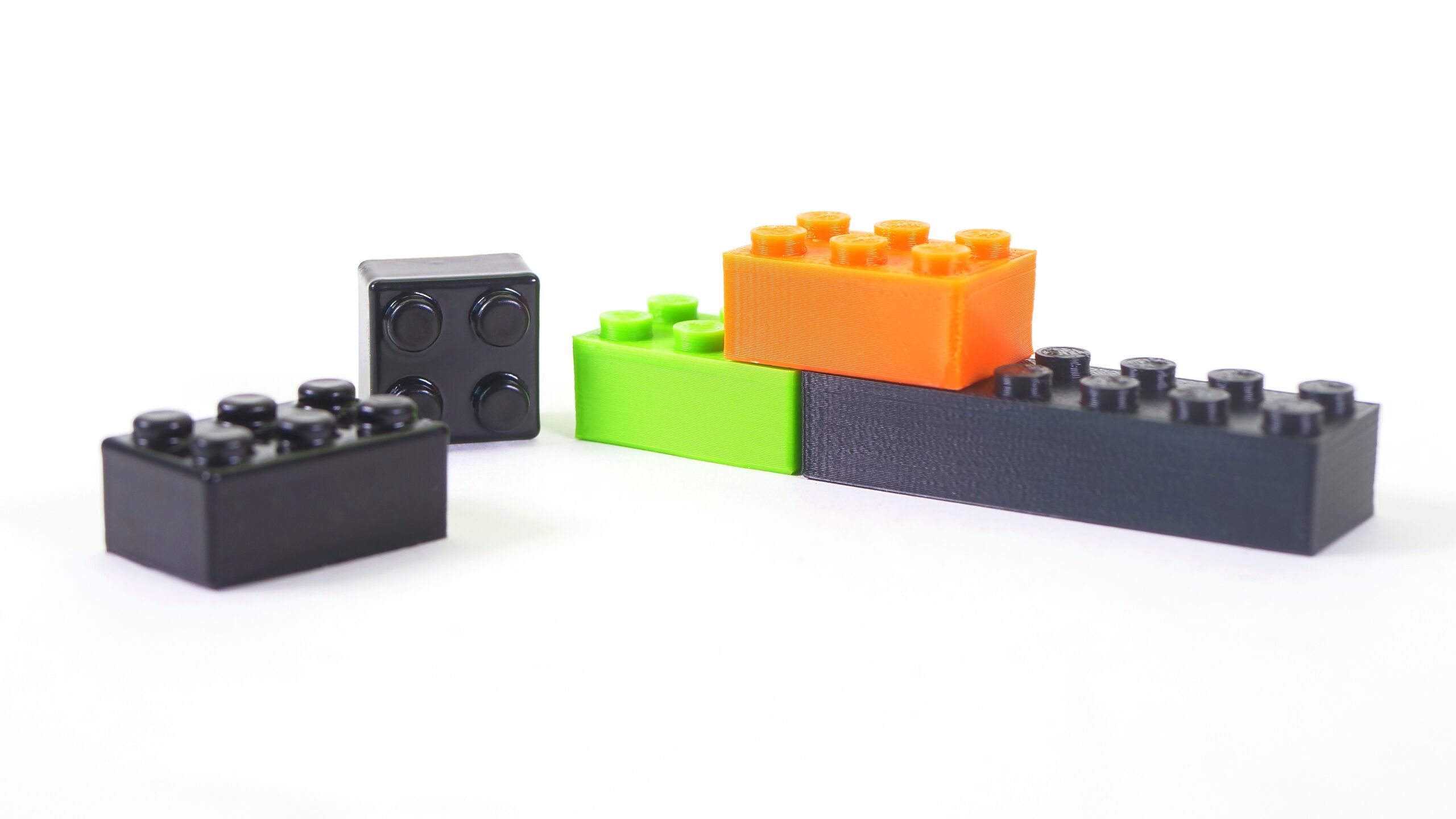
Basic info
Description
In the world of 3D printing, the ABS (Acrylonitrile Butadiene Styrene) is basically a predecessor of ASA. Some experienced users may remember it as nearly the only material available for hobby 3D printing. ABS is generally used for making inexpensive, sturdy mechanical parts (LEGO bricks, car parts, cellphone parts, etc.). The material is tenacious and high-temperature resistant. This makes it suitable for engineering parts, etc. Compared to ASA, there is slightly worse UV resistance and more significant warping and odor during printing. Note that ABS parts used outdoor turn yellowish and more brittle over time. ABS can be smoothed in aceton vapors to get a glossy, smooth finish.
To compare supported material properties, see our material table.
Pros |
Cons |
---|---|
✔ High tenacity & mechanical resistance |
✖ Significant warping |
✔ Good high-temperature resistance |
✖ Requires printer enclosure |
✔ Easy postprocessing |
✖ Potentially dangerous fumes (styrene) |
✔ Possibility of acetone smoothing and gluing | ✖ Lacks UV resistance (unlike ASA) |
Best use
The best use of ABS is for printing cheap technical parts requiring good heat and mechanical resistance or parts that need to be acetone-smoothed.
Tips for successful printing
Try to keep a high ambient temperature
The bed should be heated at least up to 100 °C, the printer should be inside an enclosure with a higher ambient temperature.
It is also possible to make your own enclosure.
If you don’t have an enclosure, there’s one simple alternative: in PrusaSlicer, go to skirt & brim and turn on the draft shield. This will keep the model slightly warmer and mitigate the warping. Printing inside an enclosure can lead to deformation of the fan shroud and other plastic parts. This can affect the printer's functionality. In case your plastic parts tend to deform, we recommend printing them from a more high-temperature resistant material, for example Prusament PC Blend.
Shrinkage
You should keep in mind that ABS-printed parts tend to shrink slightly after cooling down. We recommend printing a testing object and comparing it with a source model. The shrinkage factor of this material is usually somewhere around 1-2%.
Chemical smoothing
ABS can be sanded wet and dry and smoothed with acetone fumes, just like ASA (see more in our article about chemical smoothing)
Sample prints
![]() | ![]() |
Lego bricks | Acetone smoothed model |
3 comments
Like this you mean? https://help.prusa3d.com/en/materials
The articles for the steel sheets should also see an update very soon.