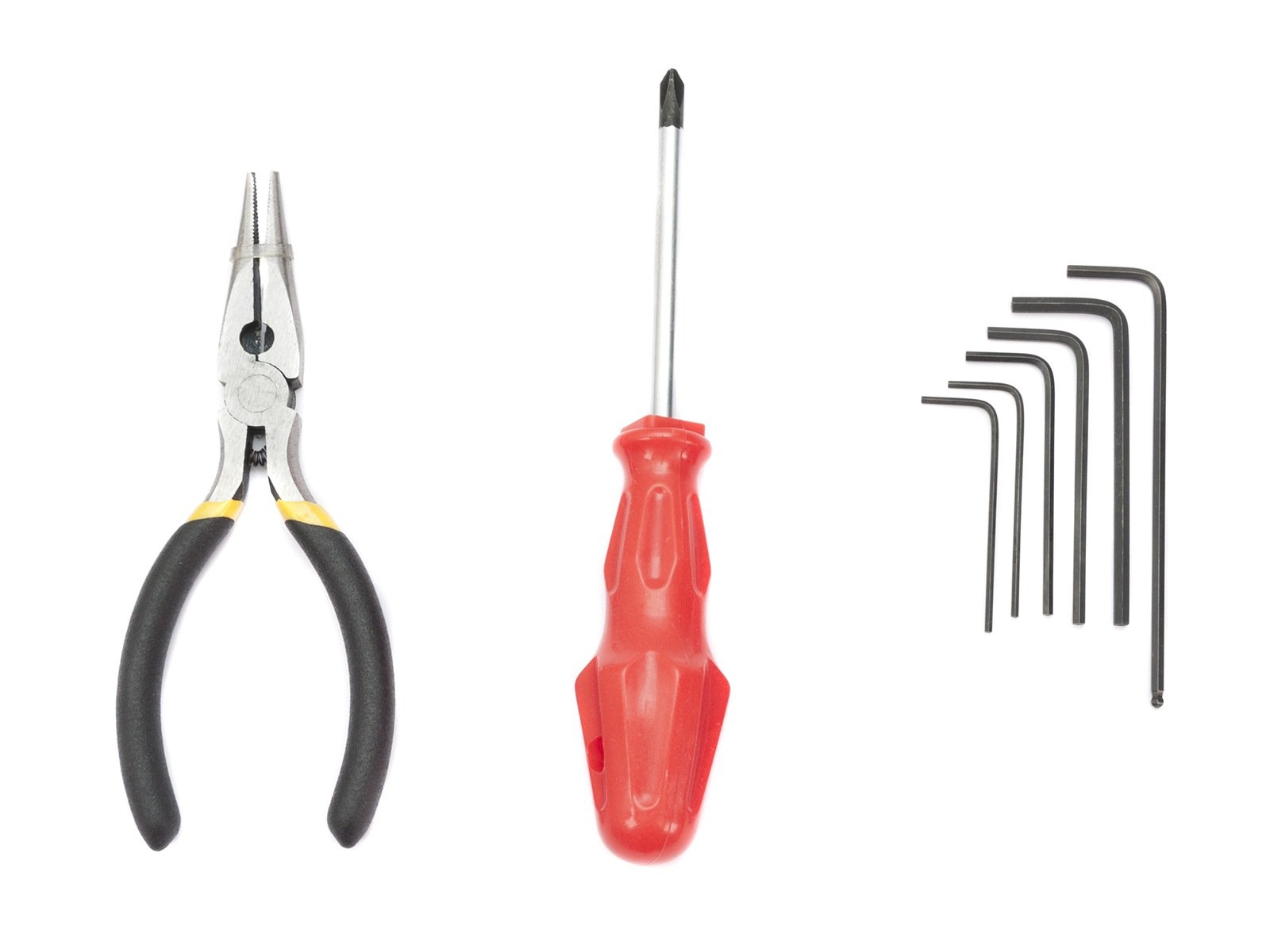
⬢Needle-nose pliers for zip tie trimming
⬢2.5mm Allen key for M3 screws
⬢2mm Allen key for nut alignment
⬢1.5mm Allen key for M2 screw
If you have printed the fan-shroud yourself, it prints out together with the inner support which needs to be removed first.
If you have a question about something that isn't covered here, check out our additional resources.
And if that doesn't do the trick, you can send an inquiry to [email protected] or through the button below.